UFR 3-04 Test Case: Difference between revisions
David.Fowler (talk | contribs) |
m (Dave.Ellacott moved page Gold:UFR 3-04 Test Case to UFR 3-04 Test Case over redirect) |
||
(44 intermediate revisions by 4 users not shown) | |||
Line 1: | Line 1: | ||
{{UFR|front=UFR 3-04|description=UFR 3-04 Description|references=UFR 3-04 References|testcase=UFR 3-04 Test Case|evaluation=UFR 3-04 Evaluation|qualityreview=UFR 3-04 Quality Review|bestpractice=UFR 3-04 Best Practice Advice|relatedACs=UFR 3-04 Related ACs}} | {{UFR|front=UFR 3-04|description=UFR 3-04 Description|references=UFR 3-04 References|testcase=UFR 3-04 Test Case|evaluation=UFR 3-04 Evaluation|qualityreview=UFR 3-04 Quality Review|bestpractice=UFR 3-04 Best Practice Advice|relatedACs=UFR 3-04 Related ACs}} | ||
Line 17: | Line 16: | ||
== Brief description of the study test case == | == Brief description of the study test case == | ||
The experimental facility consists of an open-circuit wind tunnel equipped with | The experimental facility consists of an open-circuit wind tunnel equipped with a linear blade cascade. The blade cascade consisted of five blades and the measurements were performed on the middle one. The profile N3-60 applied in the research is an industrial one and it was used as a stator vane of high-pressure part of TK-200 turbine produced by Polish manufacturer (formerly ZAMECH now ABB ALSTOM). The tested profile is scaled 3.4 times to the original one. The main geometrical parameters of the cascade were: the blade chord length ''b<sub>s</sub>''=300 mm, the pitch ''t<sub>s</sub>''=240 mm, and the blade staggered angle ''α<sub>s</sub>''=43°35′. These values according to the results of research program performed previously at the Institute of Thermal Machinery TU of Częstochowa were found to give the lowest profile losses. | ||
Positions of control planes as well as location of boundary layer traverses have been shown in Fig. 2 and 3, which may be found at http://tajfun.imc.pcz.czest.pl/transpret/. The most important flow and geometrical parameters are gathered in the Table 1. The Data Base was created under the TRANSPRETURB Thematic Network on Transition Project (EC Contract ERBICT 20-CT98-0005). | |||
Application of a movable grid located upstream the cascade entrance enabled to control the freestream turbulence intensity T<sub>u</sub> in a wide range from 0.5 to 9%. For present experiment the location of the grid was adjusted to obtain T<sub>u</sub>=4%. The outlet velocity from the cascade was kept constant at ''c<sub>2</sub>''=30 m/s that for the tested blades corresponded to a Reynolds number equal to Re= ''c<sub>2</sub>·b<sub>s</sub>/ν''= 6x10<sup>5</sup>. The inlet velocity on the cascade was equal to 9.7 m/s. | |||
< | <center><font size="3">'''Table 1'''</font></center> | ||
{| | <center> | ||
|- | {| width="482" border="1" cellspacing="1" cellpadding="4" | ||
| | |- | ||
< | | colspan="2" width="235" height="16" | | ||
| | <font size="3">'''Kinematic parameters'''</font> | ||
< | | colspan="2" width="225" | | ||
|- | <font size="3">'''Geometrical parameters'''</font> | ||
| | |- | ||
< | | width="146" height="18" | | ||
| | <font size="2">Inlet velocity on blade cascade</font> | ||
< | | width="81" | | ||
| | <font size="3"><font size="2">c</font><sub><font size="2">0</font></sub><font size="2"> = 9.7 [m/s]</font></font> | ||
< | | width="137" | | ||
| | <font size="2">Chord</font> | ||
< | | width="80" | | ||
|- | <font size="3"><font size="2">b</font><sub><font size="2">S</font></sub><font size="2"> = 300 [mm]</font></font> | ||
| | |- | ||
< | | width="146" height="18" | | ||
| | <font size="2">Outlet velocity from blade cascade</font> | ||
< | | width="81" | | ||
| | <font size="3"><font size="2">c</font><sub><font size="2">1 </font></sub><font size="2"><nowiki>= 30 [m/s]</nowiki></font></font> | ||
< | | width="137" | | ||
| | <font size="2">Axial chord</font> | ||
< | | width="80" | | ||
|- | <font size="3"><font size="2">b</font><sub><font size="2">x</font></sub><font size="2"> = 203.65 [mm]</font></font> | ||
| | |- | ||
< | | width="146" height="18" | | ||
| | <font size="2">Reynolds number</font> | ||
< | | width="81" | | ||
| | <font size="3"><font size="2">Re = 6·10</font><sup><font size="2">5</font></sup></font> | ||
< | | width="137" | | ||
| | <font size="2">Blade pitch</font> | ||
< | | width="80" | | ||
<font size="3"><font size="2">t</font><sub><font size="2">S</font></sub><font size="2"> = 240 [mm]</font></font> | |||
|- | |||
| width="146" height="18" | | |||
<font size="3"><font size="2">Freestream turbulence Tu</font><sub><font size="2">0</font></sub><font size="2"> </font></font> | |||
< | |||
< | |||
|- | |||
| | |||
< | |||
< | <font size="2">(LOW) and (HIGH)</font> | ||
| | | width="81" | | ||
< | <font size="2">4 %</font> | ||
| | | width="137" | | ||
< | <font size="2">Span</font> | ||
| | | width="80" | | ||
< | <font size="3"><font size="2">l</font><sub><font size="2">S</font></sub><font size="2"> = 250 [mm]</font></font> | ||
|- | |- | ||
| colspan="2" width="235" height="18" | | |||
< | <font size="3">'''Sampling parameters'''</font> | ||
| | | width="137" | | ||
< | <font size="2">Stagger blade angle</font> | ||
| | | width="80" | | ||
< | α<font size="3"><sub><font size="2">s</font></sub><font size="2"> = 43</font><font face="Symbol, serif"><font size="2">°</font></font><font size="2">35’</font></font> | ||
|- | |||
< | | width="146" height="18" | | ||
|- | <font size="2">Number of samples</font> | ||
| | | width="81" | | ||
< | <font size="2">750 000</font> | ||
| | | width="137" | | ||
< | <font size="2">Inlet flow angle</font> | ||
| | | width="80" | | ||
< | α<font size="3"><sub><font size="2">0</font></sub><font size="2"> = 90</font><font face="Symbol, serif"><font size="2">°</font></font></font> | ||
| | |- | ||
| width="146" height="18" | | |||
< | <font size="2">Time of sampling</font> | ||
| width="81" | | |||
< | <font size="2">30 [s]</font> | ||
| width="137" | | |||
<font size="2"> —</font> | |||
| width="80" | | |||
< | <font size="2">—</font> | ||
|- | |- | ||
| | | width="146" height="17" | | ||
< | <font size="2">Sampling frequency</font> | ||
| | | width="81" | | ||
< | <font size="2">25 [kHz]</font> | ||
| | | width="137" | | ||
< | <font size="1">—</font> | ||
| | | width="80" | | ||
< | <font size="2">—</font> | ||
|- | |||
| | |||
< | |||
| | |||
< | |||
| | |||
< | |||
| | |||
< | |||
|} | |} | ||
</center> | |||
<center>[[Image:U3-04d32_files_image004.gif]]</center> | |||
< | <center>[[Image:U3-04d32_files_image006.gif]]</center> | ||
The analysis of pressure loss distribution along the blade height shown in Fig. 1 reveals that a substantial portion of flow is free from secondary losses. Measurements were performed in the middle of the blade height that allows to treat the problem analysed as a two-dimensional one. To confirm this conclusion the oil surface visualization on the suction side of the blade was performed (see Fig. 2). The evolution of the secondary flows, bounded by the red dashed lines, is well seen, so one can conclude that the flow in the middle of the blade is not disturbed by their influence. The oil visualization shows also the small separation line, which is located just after minimum pressure point (for surface coordinate S<sub>s</sub>=0.55). This last observation is important in the connection with the analysis of the boundary layer development discussed in chapter 6. It is worth to mention, that since single-wire probe was applied no correction on momentum and energy balance was possible. | |||
== Test Case Experiments == | == Test Case Experiments == | ||
Line 144: | Line 123: | ||
Additionally, wall shear stresses have been measured with the use of surface mounted hot-film techniques. Because the in-situ calibration of surfaces gauges was not possible, it was decided to apply the semi-quantitative approach (Hodson, 1983), where the wall shear stresses have been calculated according to the formula | Additionally, wall shear stresses have been measured with the use of surface mounted hot-film techniques. Because the in-situ calibration of surfaces gauges was not possible, it was decided to apply the semi-quantitative approach (Hodson, 1983), where the wall shear stresses have been calculated according to the formula | ||
In this equation it was assumed that the rate of heat loss to the substrate, could be approximated using the square of voltage E<sub>0</sub> for non-flow conditions and that the temperature difference was proportional to E<sub>0</sub><sup>2</sup>. For the present investigation the magnitude of E<sub>0</sub> was controlled before and after data acquisition. The units associated with the quantity ω<sub>w</sub> are arbitrary, but this procedure allows the relative signals from individual gauges to be compared. During the experiment DANTEC hot-film gauge of 55R47 type has been used. | <center><math>\tau_w\propto\left(\frac{E^2-E_0^2}{E_0^2}\right)^3</math></center> | ||
In this equation it was assumed that the rate of heat loss to the substrate, could be approximated using the square of voltage ''E<sub>0</sub>'' for non-flow conditions and that the temperature difference was proportional to ''E<sub>0</sub><sup>2</sup>''. For the present investigation the magnitude of ''E<sub>0</sub> ''was controlled before and after data acquisition. The units associated with the quantity ''ω<sub>w</sub>'' are arbitrary, but this procedure allows the relative signals from individual gauges to be compared. During the experiment DANTEC hot-film gauge of 55R47 type has been used. | |||
The uncertainty analysis of recorded signal revealed a measuring error of 10% for hot-wire signals and 15% for hot-films signals. | The uncertainty analysis of recorded signal revealed a measuring error of 10% for hot-wire signals and 15% for hot-films signals. | ||
Line 152: | Line 133: | ||
== CFD Methods == | == CFD Methods == | ||
The numerical analysis has been performed with the use of the unsteady UNNEWT+PUIM solver (Vilmin | The numerical analysis has been performed with the use of the unsteady UNNEWT+PUIM solver (Vilmin ''et al'', 2002). The code UNNEWT is an unsteady version of the unstructured-mesh viscous flow solver NEWT (Dawes, 1992). The governing equations are discretised in space using the vertex based scheme with overlapping control-volumes, with fluxes being computed through the faces of triangular cells. Time integration of the discretised equations is carried out using second order four-step explicit Runge-Kutta time-stepping scheme. The blending of second order and fourth order artificial dissipation is used to damp numerical oscillations. The turbulence model used is the low-Reynolds number Yang and Shih k-ε model (Yang and Shih, 1993), with damping functions in the near-wall regions. In this model k<sup>1/2 </sup>is chosen as the turbulent velocity scale. The time scale T<sub>t</sub> is bounded from below by the Kolmogorov time scale [[Image:U3-04d32_files_image010.gif]]. That is why when this time scale is used to reformulate the dissipation equation, there is no singularity at the wall and so the introduction of a pseudo-dissipation rate is avoided. The model constants are exactly the same as those in the standard k-ε model, which ensures correct performance of the model far from the wall. A damping function is proposed as a function of | ||
<math>\text{Re}_y = \frac{k^\frac{1}{2}y}{\nu}</math>, so in this way the only damping function in this model, which is introduced to eddy viscosity formula is free from any geometrical parameter. | |||
To avoid overprediction of a turbulent kinetic energy in the stagnation regions (inherent phenomena of two equation models), the treatment introduced by Durbin (Durbin, 1996) has been applied. His proposition is to bound the turbulent time-scale in the stagnation region and in this way to increase the level of dissipation there. | To avoid overprediction of a turbulent kinetic energy in the stagnation regions (inherent phenomena of two equation models), the treatment introduced by Durbin (Durbin, 1996) has been applied. His proposition is to bound the turbulent time-scale in the stagnation region and in this way to increase the level of dissipation there. | ||
Reliable modeling of transitional flows is possible with the use of prescribed unsteady intermittency method PUIM (Schulte and Hodson, 1998). The PUIM calculates a distance-time intermittency field (constant in time in the case of steady flow simulation). The intermittency factor is imposed on the k-ε turbulence model at streamwise wall stations, which acts as a multiplier of the eddy viscosity in the diffusive terms of the transport equations in the laminar regions (Vilmin | Reliable modeling of transitional flows is possible with the use of prescribed unsteady intermittency method PUIM (Schulte and Hodson, 1998). The PUIM calculates a distance-time intermittency field (constant in time in the case of steady flow simulation). The intermittency factor is imposed on the k-ε turbulence model at streamwise wall stations, which acts as a multiplier of the eddy viscosity in the diffusive terms of the transport equations in the laminar regions (Vilmin ''et al'', 2002). During the time marching process, the PUIM routines are called regularly. The number of iterations between two calls is fixed by the user in the run parameters file. The intermittency distribution is calculated based on empirical correlations for transition on-set and spot production rate spreading of the spot. The laminar-turbulent transition onset is determined using the Mayle’s correlation (Mayle, 1991), which depends on the turbulence intensity at the boundary-layer edge. The correlation used for the spot production rate is correlation of Mayle (Mayle, 1991) or Gostelow and Walker (Gostelow and Walker, 1996). Both these correlations depend on the pressure gradient and turbulence intensity. The intermittency factor in PUIM is computed either using the concentrated breakdown concept of Narasimha (1957), or using a continuous breakdown of the turbulent spots that accounts for the properties of the calmed region (Ramesh and Hodson, 1999). | ||
The applied here experimental correlations are: | The applied here experimental correlations are: | ||
* for prediction of transition onset (Mayle, 1991) [[Image:U3-04d32_files_image014.gif]] | |||
* for prediction of transition onset (Abu-Ghannam and Shaw, 1980) [[Image:U3-04d32_files_image016.gif]] | |||
* for the spot production rate in an attached flow (Mayle, 1991) | |||
[[Image:U3-04d32_files_image018.gif]] for zero pressure gradient | |||
[[Image:U3-04d32_files_image020.gif]] for favourable pressure gradient | |||
[[Image:U3-04d32_files_image022.gif]] for adverse pressure gradient | |||
* for spreading of the spots (Gostelow and Walker, 1992) | |||
[[Image:U3-04d32_files_image024.gif]] | |||
where: | where: | ||
Re<sub | Re<sub>q</sub> - critical Reynolds number | ||
''Tu'' | ''Tu'' — turbulence intensity | ||
g<sub>tr </sub>- spot formation rate | g<sub>tr </sub>- spot formation rate | ||
< | s - spot propagation parameter | ||
λ<sub>θ</sub>- Thwaites pressure gradient parameter | |||
<center>[[Image:U3-04d32_files_image026.gif]]</center> | |||
Along the viscous surface, the nonslip condition is imposed for values y<sup>+</sup> under 10. Otherwise a wall slip condition is used. In the wall viscous regions damping function, which is a function of <math>\text{Re}_y=\frac{k^\frac{1}{2}y}{\nu}</math> is applied. As the inlet boundary conditions, the total pressure, the total temperature and the flow angle are fixed, while at outlet the static pressure extrapolated from the interior is kept constant. | |||
The computational domain developed around the tested blade was bounded by inlet plane located 70 mm upstream the leading edge and outlet plane located 140 mm downstream the trailing edge of the blade. Additionally, the periodical planes have been situated 120 mm above and 120 mm below the blade what corresponds to 1/2 of blade pitch. The triangular based unstructured mesh has been developed and consisted of 6580 nodes. To capture the phenomena in boundary layer the density of the mesh has been increased in the direction towards the wall (Fig. 3). The wall adjacent grid cells with the aspect ratio 1:56 are located at a distance y+=0.4 (0.05 mm). There is about 22 grid cells within boundary layer all around the blade profile. | The computational domain developed around the tested blade was bounded by inlet plane located 70 mm upstream the leading edge and outlet plane located 140 mm downstream the trailing edge of the blade. Additionally, the periodical planes have been situated 120 mm above and 120 mm below the blade what corresponds to 1/2 of blade pitch. The triangular based unstructured mesh has been developed and consisted of 6580 nodes. To capture the phenomena in boundary layer the density of the mesh has been increased in the direction towards the wall (Fig. 3). The wall adjacent grid cells with the aspect ratio 1:56 are located at a distance y+=0.4 (0.05 mm). There is about 22 grid cells within boundary layer all around the blade profile. | ||
The numerical simulations were performed for the Reynolds number Re=600,000 and for the outlet Mach number Ma= 0.3. The Mach number as well as the inflow and outflow velocity was increased 3.4 times to speed up the calculations but nevertheless the flow still could be considered as incompressible. At the inlet the following parameters were adjusted: turbulence intensity Tu=3.8%, the length scale | The numerical simulations were performed for the Reynolds number Re=600,000 and for the outlet Mach number Ma= 0.3. The Mach number as well as the inflow and outflow velocity was increased 3.4 times to speed up the calculations but nevertheless the flow still could be considered as incompressible. At the inlet the following parameters were adjusted: turbulence intensity Tu=3.8%, the length scale λ= 3mm, inlet stagnation pressure P<sub>s</sub>=28800 Pa, inlet stagnation temperature 293.2 °K, what was identical with experimental conditions. The static pressure at the outlet was kept constant. | ||
<center>[[Image:U3-04d32_files_image031.gif]]</center> | |||
The numerical analysis of the flow around the blade was preceded by the analysis of the grid quality in the boundary layer region. The grid independence tests have been performed on three meshes of the similar type, where the only difference was the number of mesh cells across boundary layer. The number of cells for consecutive meshes was 10, 20, 25 cells, which suits the adequately total number of nodes equal 4470, 6580, 8290. Fig.4 presents the comparison of calculated velocity profiles with superimposed experimental data for 69% and 71% distance of the suction side. As it could be seen the number of cells of the order 20 is sufficient to reproduce the velocity distribution within the boundary layer. It means also that the quality of the grid is good enough and that the transition location should not depend on its resolution. It was decided that the medium density grid will be kept in all further calculations. | |||
<font size="-2" color="#888888">© copyright ERCOFTAC 2004</font><br /> | <font size="-2" color="#888888">© copyright ERCOFTAC 2004</font><br /> | ||
Line 204: | Line 194: | ||
{{UFR|front=UFR 3-04|description=UFR 3-04 Description|references=UFR 3-04 References|testcase=UFR 3-04 Test Case|evaluation=UFR 3-04 Evaluation|qualityreview=UFR 3-04 Quality Review|bestpractice=UFR 3-04 Best Practice Advice|relatedACs=UFR 3-04 Related ACs}} | {{UFR|front=UFR 3-04|description=UFR 3-04 Description|references=UFR 3-04 References|testcase=UFR 3-04 Test Case|evaluation=UFR 3-04 Evaluation|qualityreview=UFR 3-04 Quality Review|bestpractice=UFR 3-04 Best Practice Advice|relatedACs=UFR 3-04 Related ACs}} | ||
Latest revision as of 12:43, 12 February 2017
Laminar-turbulent boundary layer transition
Underlying Flow Regime 3-04 © copyright ERCOFTAC 2004
Test Case
Brief description of the study test case
The experimental facility consists of an open-circuit wind tunnel equipped with a linear blade cascade. The blade cascade consisted of five blades and the measurements were performed on the middle one. The profile N3-60 applied in the research is an industrial one and it was used as a stator vane of high-pressure part of TK-200 turbine produced by Polish manufacturer (formerly ZAMECH now ABB ALSTOM). The tested profile is scaled 3.4 times to the original one. The main geometrical parameters of the cascade were: the blade chord length bs=300 mm, the pitch ts=240 mm, and the blade staggered angle αs=43°35′. These values according to the results of research program performed previously at the Institute of Thermal Machinery TU of Częstochowa were found to give the lowest profile losses.
Positions of control planes as well as location of boundary layer traverses have been shown in Fig. 2 and 3, which may be found at http://tajfun.imc.pcz.czest.pl/transpret/. The most important flow and geometrical parameters are gathered in the Table 1. The Data Base was created under the TRANSPRETURB Thematic Network on Transition Project (EC Contract ERBICT 20-CT98-0005).
Application of a movable grid located upstream the cascade entrance enabled to control the freestream turbulence intensity Tu in a wide range from 0.5 to 9%. For present experiment the location of the grid was adjusted to obtain Tu=4%. The outlet velocity from the cascade was kept constant at c2=30 m/s that for the tested blades corresponded to a Reynolds number equal to Re= c2·bs/ν= 6x105. The inlet velocity on the cascade was equal to 9.7 m/s.
Kinematic parameters |
Geometrical parameters | ||
Inlet velocity on blade cascade |
c0 = 9.7 [m/s] |
Chord |
bS = 300 [mm] |
Outlet velocity from blade cascade |
c1 = 30 [m/s] |
Axial chord |
bx = 203.65 [mm] |
Reynolds number |
Re = 6·105 |
Blade pitch |
tS = 240 [mm] |
Freestream turbulence Tu0 (LOW) and (HIGH) |
4 % |
Span |
lS = 250 [mm] |
Sampling parameters |
Stagger blade angle |
αs = 43°35’ | |
Number of samples |
750 000 |
Inlet flow angle |
α0 = 90° |
Time of sampling |
30 [s] |
— |
— |
Sampling frequency |
25 [kHz] |
— |
— |
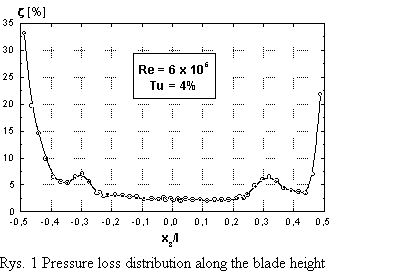
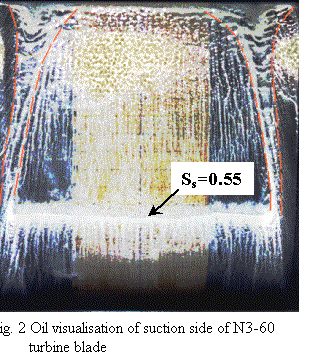
The analysis of pressure loss distribution along the blade height shown in Fig. 1 reveals that a substantial portion of flow is free from secondary losses. Measurements were performed in the middle of the blade height that allows to treat the problem analysed as a two-dimensional one. To confirm this conclusion the oil surface visualization on the suction side of the blade was performed (see Fig. 2). The evolution of the secondary flows, bounded by the red dashed lines, is well seen, so one can conclude that the flow in the middle of the blade is not disturbed by their influence. The oil visualization shows also the small separation line, which is located just after minimum pressure point (for surface coordinate Ss=0.55). This last observation is important in the connection with the analysis of the boundary layer development discussed in chapter 6. It is worth to mention, that since single-wire probe was applied no correction on momentum and energy balance was possible.
Test Case Experiments
Experimental investigations of velocity field in the boundary layer have been performed using a single wire probe combined with the DISA 55M System hot-wire anemometer coupled to PC computer. The computer was equipped with 12-bit analog-digital (A/D) converter with the input range 0-12V. The hot-wire was calibrated in-situ before and after the experiment. Detailed measurements of boundary layer characteristics were performed in 54 cross-sections distributed along the suction and pressure sides of tested profile. At each station, the boundary layer was penetrated in 30-40 locations where a 40 sec signal was sampled with 25 kHz frequency.
Additionally, wall shear stresses have been measured with the use of surface mounted hot-film techniques. Because the in-situ calibration of surfaces gauges was not possible, it was decided to apply the semi-quantitative approach (Hodson, 1983), where the wall shear stresses have been calculated according to the formula
In this equation it was assumed that the rate of heat loss to the substrate, could be approximated using the square of voltage E0 for non-flow conditions and that the temperature difference was proportional to E02. For the present investigation the magnitude of E0 was controlled before and after data acquisition. The units associated with the quantity ωw are arbitrary, but this procedure allows the relative signals from individual gauges to be compared. During the experiment DANTEC hot-film gauge of 55R47 type has been used.
The uncertainty analysis of recorded signal revealed a measuring error of 10% for hot-wire signals and 15% for hot-films signals.
CFD Methods
The numerical analysis has been performed with the use of the unsteady UNNEWT+PUIM solver (Vilmin et al, 2002). The code UNNEWT is an unsteady version of the unstructured-mesh viscous flow solver NEWT (Dawes, 1992). The governing equations are discretised in space using the vertex based scheme with overlapping control-volumes, with fluxes being computed through the faces of triangular cells. Time integration of the discretised equations is carried out using second order four-step explicit Runge-Kutta time-stepping scheme. The blending of second order and fourth order artificial dissipation is used to damp numerical oscillations. The turbulence model used is the low-Reynolds number Yang and Shih k-ε model (Yang and Shih, 1993), with damping functions in the near-wall regions. In this model k1/2 is chosen as the turbulent velocity scale. The time scale Tt is bounded from below by the Kolmogorov time scale . That is why when this time scale is used to reformulate the dissipation equation, there is no singularity at the wall and so the introduction of a pseudo-dissipation rate is avoided. The model constants are exactly the same as those in the standard k-ε model, which ensures correct performance of the model far from the wall. A damping function is proposed as a function of
, so in this way the only damping function in this model, which is introduced to eddy viscosity formula is free from any geometrical parameter.
To avoid overprediction of a turbulent kinetic energy in the stagnation regions (inherent phenomena of two equation models), the treatment introduced by Durbin (Durbin, 1996) has been applied. His proposition is to bound the turbulent time-scale in the stagnation region and in this way to increase the level of dissipation there.
Reliable modeling of transitional flows is possible with the use of prescribed unsteady intermittency method PUIM (Schulte and Hodson, 1998). The PUIM calculates a distance-time intermittency field (constant in time in the case of steady flow simulation). The intermittency factor is imposed on the k-ε turbulence model at streamwise wall stations, which acts as a multiplier of the eddy viscosity in the diffusive terms of the transport equations in the laminar regions (Vilmin et al, 2002). During the time marching process, the PUIM routines are called regularly. The number of iterations between two calls is fixed by the user in the run parameters file. The intermittency distribution is calculated based on empirical correlations for transition on-set and spot production rate spreading of the spot. The laminar-turbulent transition onset is determined using the Mayle’s correlation (Mayle, 1991), which depends on the turbulence intensity at the boundary-layer edge. The correlation used for the spot production rate is correlation of Mayle (Mayle, 1991) or Gostelow and Walker (Gostelow and Walker, 1996). Both these correlations depend on the pressure gradient and turbulence intensity. The intermittency factor in PUIM is computed either using the concentrated breakdown concept of Narasimha (1957), or using a continuous breakdown of the turbulent spots that accounts for the properties of the calmed region (Ramesh and Hodson, 1999).
The applied here experimental correlations are:
- for the spot production rate in an attached flow (Mayle, 1991)
for favourable pressure gradient
- for spreading of the spots (Gostelow and Walker, 1992)
where:
Req - critical Reynolds number
Tu — turbulence intensity
gtr - spot formation rate
s - spot propagation parameter
λθ- Thwaites pressure gradient parameter
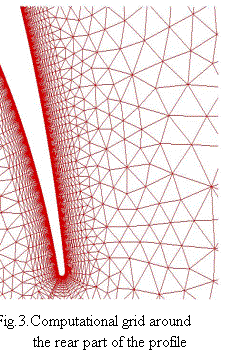
Along the viscous surface, the nonslip condition is imposed for values y+ under 10. Otherwise a wall slip condition is used. In the wall viscous regions damping function, which is a function of is applied. As the inlet boundary conditions, the total pressure, the total temperature and the flow angle are fixed, while at outlet the static pressure extrapolated from the interior is kept constant.
The computational domain developed around the tested blade was bounded by inlet plane located 70 mm upstream the leading edge and outlet plane located 140 mm downstream the trailing edge of the blade. Additionally, the periodical planes have been situated 120 mm above and 120 mm below the blade what corresponds to 1/2 of blade pitch. The triangular based unstructured mesh has been developed and consisted of 6580 nodes. To capture the phenomena in boundary layer the density of the mesh has been increased in the direction towards the wall (Fig. 3). The wall adjacent grid cells with the aspect ratio 1:56 are located at a distance y+=0.4 (0.05 mm). There is about 22 grid cells within boundary layer all around the blade profile.
The numerical simulations were performed for the Reynolds number Re=600,000 and for the outlet Mach number Ma= 0.3. The Mach number as well as the inflow and outflow velocity was increased 3.4 times to speed up the calculations but nevertheless the flow still could be considered as incompressible. At the inlet the following parameters were adjusted: turbulence intensity Tu=3.8%, the length scale λ= 3mm, inlet stagnation pressure Ps=28800 Pa, inlet stagnation temperature 293.2 °K, what was identical with experimental conditions. The static pressure at the outlet was kept constant.
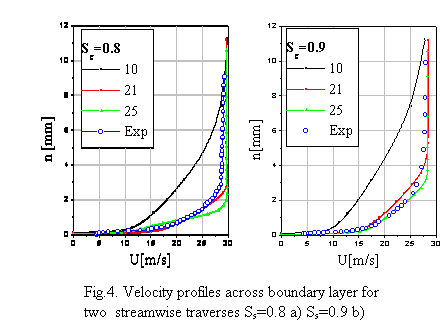
The numerical analysis of the flow around the blade was preceded by the analysis of the grid quality in the boundary layer region. The grid independence tests have been performed on three meshes of the similar type, where the only difference was the number of mesh cells across boundary layer. The number of cells for consecutive meshes was 10, 20, 25 cells, which suits the adequately total number of nodes equal 4470, 6580, 8290. Fig.4 presents the comparison of calculated velocity profiles with superimposed experimental data for 69% and 71% distance of the suction side. As it could be seen the number of cells of the order 20 is sufficient to reproduce the velocity distribution within the boundary layer. It means also that the quality of the grid is good enough and that the transition location should not depend on its resolution. It was decided that the medium density grid will be kept in all further calculations.
© copyright ERCOFTAC 2004
Contributors: Andrzej Boguslawski - Technical University of Czestochowa